一、案例简介
冲压件智能生产建设项目基于冲压件领域智能化装备提升和物联网技术应用,主要从实施全流程生产工艺全“机器换人”工程来提升车间全自动化生产水平,从实施ERP系统、全车间设备数据采集系统等几个方面开展智能化改造提升信息化、数字化、智能化发展水平。通过以上智能化改造,公司目前员工人数已下降了25%,生产效率提高了35%,产品不良品率降低了32%,公司整体运营成本降低25%。
二、项目内容
根据公司未来三年坚持总体规划、分步实施、业务引领、先行先试的方针进行智能制造升级。首先从整个企业发展战略出发,制定符合企业长期发展方向的智能制造发展规划,在此基础上,根据实际业务需求,分步骤实现各项规划内容。
第一步,实施全流程“机器换人”工程,提升车间全自动生产流程,进一步提高生产效率。主要包括实施数控等离子切割机、高频淬火炉、大型卷板机、大吨位压力机、大型自动焊机等千先进生产设备等关键生产流程设备“机器换人”。利用自动化机器人在焊接、包装流程实现企业生产提质降本,提高现场的管理能力。在前期设备情况下,项目投资1000万元,实施周期12-24个月。
第二步,规划实施ERP系统、智能车间数据采集系统等,提升信息化、数字化、智能化发展水平。
(1)实施ERP系统,直接通过工业互联网平台覆盖业务相关环节,实现管理流程的信息化。
(2)实施智能车间数据采集系统,其中“冲压件生产线数字化管控技术开发”,基于PPI\OPC\Modbus协议开发新型数据采集管控技术,能实时采集生产设备状态数据的同时完成设备的自动化参数修正并自动进行计算调度优化功能,以实现车间生产设备的预测性运维和车间数字化集中管控。
(3)设备全生命周期信息化管理系统,围绕设备的“进、出、维、修、检”各个环节进行科学管理,提供针对设备的“采购→验收→入账→养护→维修→盘点→报废”全生命周期跟踪管理,以预防性维护及预测性维修为中心,帮助企业实现设备的全面信息化管理,降低设备故障率,保持设备稳定性。
智能化车间数据采集系统已通过《智能车间数据采集系统》所确定内容,于2022年7月25日实施完成。
部分智能化改造应用场景图片展示:
(1)ERP系统
系统建设的主要内容是建设ERP系统模块,覆盖业务相关环节,实现管理流程的信息化。
(2)数采终端大屏
实施智能车间数据采集系统,实施全部设备智能化改造、联网上云,实时查看设备的当日产量、月产量、年产量、设备的运行状态、设备的工作时常。
|
| 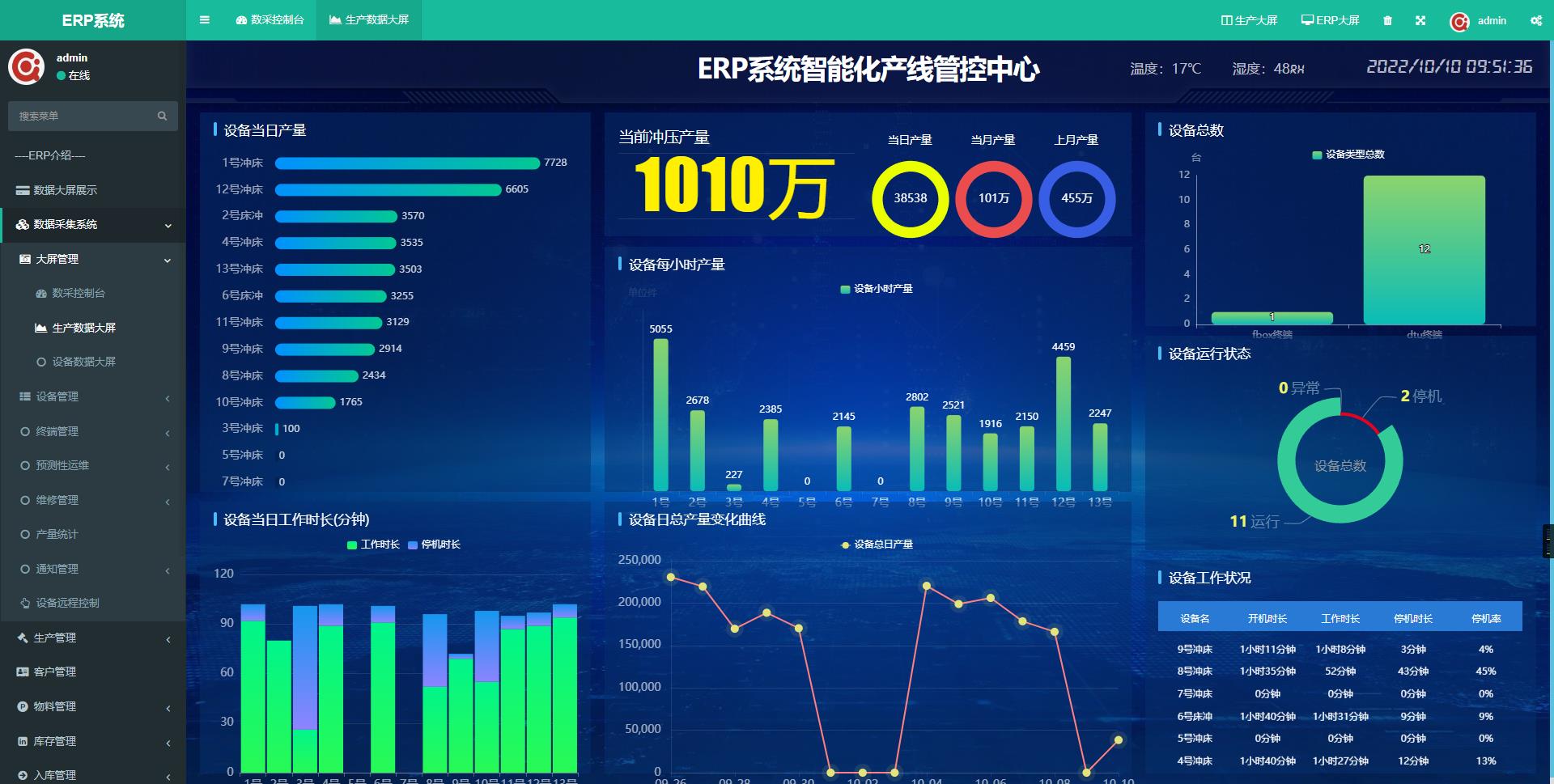 |
车间数据大屏
该模块主要包含数采设备的数量、设备的在线情况、维修保养的清单、以及车间设备报警故障的处理情况。
|
| 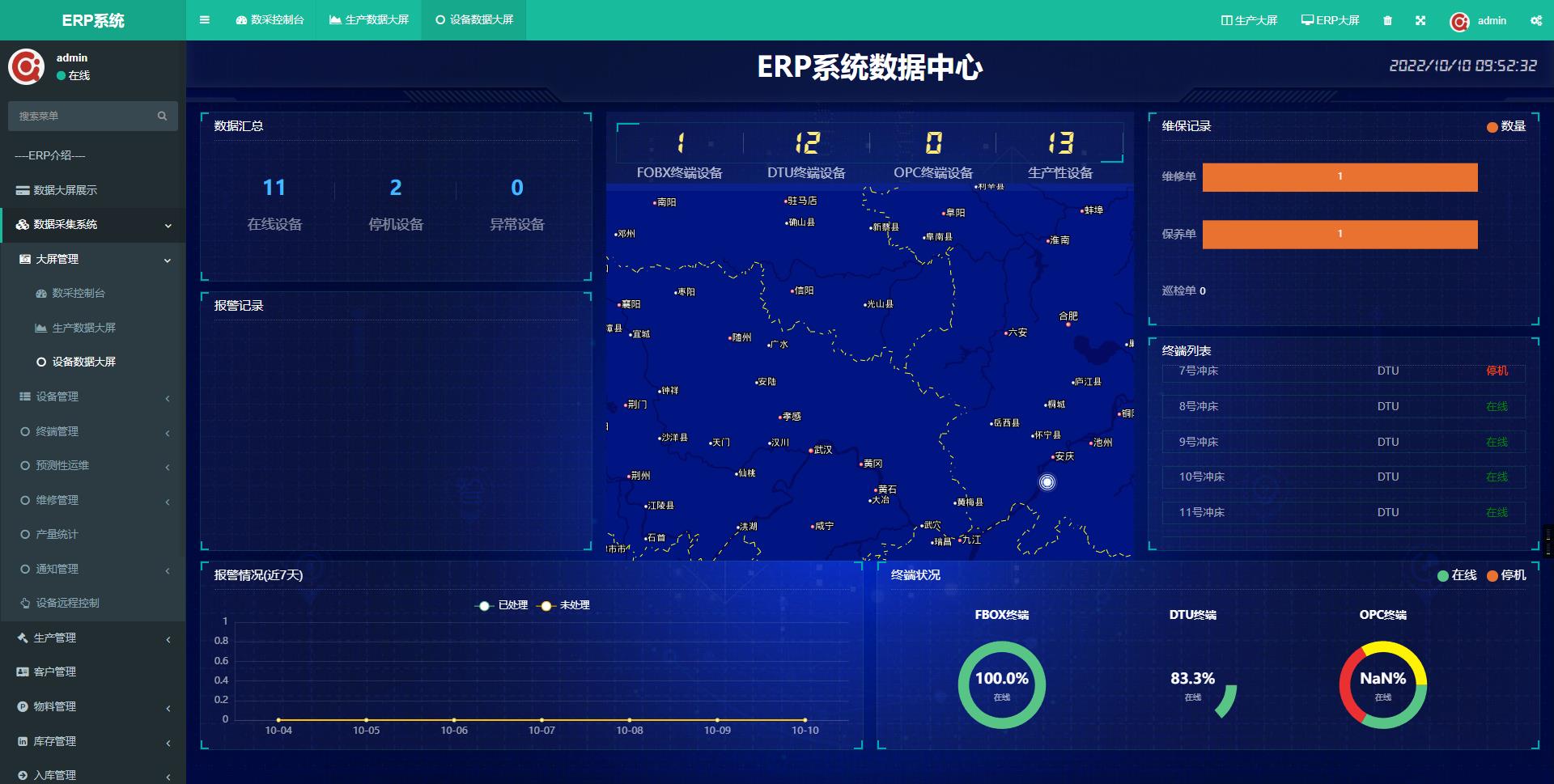 |
第三步,规划实施APS高级计划排程系统。实现对企业仓储、生产、工序、物料等生产活动的全面管控。结合自动化设备进一步提高生产效率。预算投资共30万元,实施周期预计2-3个月。
三、取得成效
对关键工序进行了自动化升级,引入大量专用自动化设备。通过实现机器自动化提升,设备间协作提升,为进一步智能化系统管理提升做了前期准备。
此后,公司重点建设了“ERP系统及智能车间数据采集系统”智能化改造项目,以工厂设备全连接和生产要素集成控制为核心目标,通过实施全车间设备数据采集系统、ERP接口对接实现数据集中展示等智能化改造,分阶段打造5G+全连接智能工厂,助力高质量发展。ERP系统实现了生产、进销存、财务、人力资源等全流程信息化;智能车间数据采集系统,实现全厂车间设备智能化改造、联网上云、远程运维,数据集中可视化展示等。
通过以上智能化改造,公司目前员工人数已下降了25%,生产效率提高了35%,产品不良品率降低了32%,公司整体运营成本降低25%。
公司将按规划,在前期智能制造现有成果基础上,对焊接、包装等关键工艺进行“机器换人”工程,并继续加大管理系统等智能化解决方案的投入,助力企业进入智能制造新阶段。。
五、亮点及模式总结
对于一个冲压企业来说,其基本工艺包括落料、折弯、拉深、成形、焊接、装配等,属于典型的离散制造。随着用工成本和管理成本的提高,同时客户对企业的要求也越来越严格,企业关注的焦点,离不开质量、成本、交期。从这个角度出发,企业如何削减用工成本,如何提高管理运营效率,如何提高质量、交期等核心竞争力,通过智能车间和数字化工厂的建设,可以给企业带来很大的帮助。
(1)现状把握,对标找差
首先从企业现状出发,做一下充分的现状调研和评估,找到企业的薄弱环节和管理差距在哪里。
对照行业标杆企业和新技术,积极参与各种标杆企业交流和学习活动,通过现场参观,标杆走访和互动交流,参考行业标杆和示范企业的做法,借鉴他们的先进设备和新技术应用,学习他们在智能化建设过程中的管理经验和教训,特别是避免犯同样的错误,这一点尤其重要,可以少走很多弯路。
(2)整体规划、顶层设计
对现状进行摸底和调研以后,明确了自身的问题点和薄弱项,之后,必须要从顶层设计的角度,对智能车间和数字化工厂的建设,进行整体规划,从宏观的角度,明确建设目标和建设的路径。
(3)企业战略和目标分解
首先,企业的整体规划,一定要同公司未来的发展战略相结合,明确公司未来3-5年甚至更长时间智能工厂的总体架构与建设目标,定义生产制造、工艺规划与设计、供应链、管理决策等核心应用的内容与业务模式转型,确定相应的支撑体系。整体架构既要充分引入和吸收国际、国内先进的制造技术,又要考虑这些技术在公司的可落地性以及可实施性。
(4)业务流程梳理和管理规则制定
其次,在具体项目的落地实施前,围绕企业的核心业务流程,企业一定要做一个完整的流程梳理,明确各个环节的业务流程和管理规则,同时定岗定责,特别是应该覆盖从订单报价、工艺设计、采购、生产计划、生产制造、质量控制、仓储物流、发货管理、设备能源管理、人力资源管理、成本核算、数据分析与系统集成等核心内容。
(5)制定切实可行的实施路线
企业必须结合现有管理基础、技术条件与未来发展,对核心应用各层级进行详细规划,定义各层级重点项目与实施路径,并规划企业全业务链中纵向与横向的集成框架体系,形成完整的智能车间和数字化工厂解决方案。
(6)分步实施、按模块分阶段落地
整体规划、顶层设计完成后,就进入到落地执行的阶段,可以应用系统演进路线图,明确各子项目实施先后顺序、实施路径、实施前提、部署方式、重点任务、落地实施计划与里程碑等。